How Packaging Manufacturers Influence Product Quality
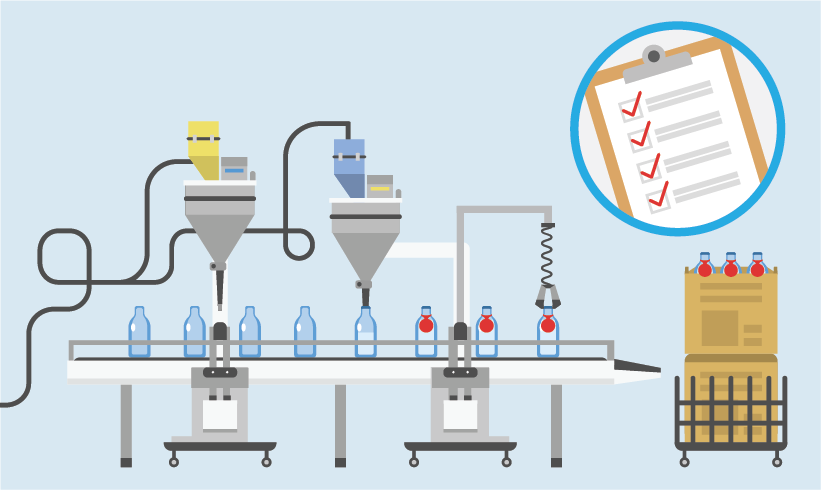
A safe, quality product should be what all manufacturers strive for. In fact, it’s probably something you or a colleague devotes their entire job to day in and day out.
Regardless of the efforts you take in your production facility, the quality of your end product can only be as good as the measures taken by each member along your supply chain.
So, how do you ensure your suppliers hold the same high standards that you do? Look for certifications.
Whether it’s packaging or another outsourced product, safety and quality certification among your supply chain members should hold high importance to your business. Sourcing materials from suppliers with industry-recognized certifications not only streamlines your ability to meet regulatory requirements, it also safeguards your brand and gives customers confidence in your product.
Quality assurance
Chances are, all the materials you need to make your product aren’t solely produced at your plant. It’s not uncommon to outsource materials like product packaging or labels, which are crucial links to getting your product off the production line and into retail stores.
It’s a system that operates much like a series of individual chains linking together to make one comprehensive chain link. If a singular link gets compromised, the whole chain gets broken. The same can be said for the quality and safety of your product.
To avoid the figurative chain from being broken, you need to carefully choose providers who are going to consistently produce a quality product as frequently as possible.
How can you tell if talk is cheap or your contracted provider will satisfactorily deliver? Request quality assurance certifications, such as ISO 9001:2015.
Designed to promote a continuous loop of self-evaluation and improvement, ISO 9001-certified companies establish a set of quality objectives they strive to meet. Their customers and the ISO-certifying body hold them to it.
“ISO 9001:2015 sets a global standard for Quality Management Systems and ensures their efficiency for products, services, and international supply chains.” – Quality Magazine
Certificate holders are rigorously audited to prove that their processes are followed by everyone in the organization, which decreases your chance of receiving a defective product and slowing down your production line.
Food safety
If you’re a food provider, there are additional considerations as to what makes a “quality” product.
Among the top of the list? Food safety.
Protecting your consumers and your brand is paramount. Accomplishing that takes additional effort and care beyond meeting regulatory requirements from you and all your suppliers.
“Food safety is important at every stage of the food supply chain. It protects consumers, meets legal obligations and safeguards your brand.” – Intertek
There are a number of food safety or quality certification schemes that are recognized by the Global Food Standards Initiative, including: BRC Global Standard, SQF, FSSC 2000, and International Featured Standards. These or similar certifications satisfy the audit you are required to conduct upon your suppliers.
While your ability to forgo a physical plant audit saves you time and money, there are more benefits for you to reap by managing a supply chain that adheres to globally-recognized food safety standards.
Because some retailers require proof of GFSI compliance, maintaining a food-safe supply chain could also help your business enter into new markets. More markets = more brand exposure = more $.
Because certificate holders adhere to strict regulatory safety and labeling requirements, your risk of product recall will be reduced upon sourcing your product packaging and other secondary materials from a company who is audited against the standards set by GSFI.
“The global standard for food safety will ensure your customers have confidence in your production programs and supply chain management.” – BRCGS
Save the headache
The certifications, or lack thereof, should be just as an important deciding factor as product cost as you do your due diligence in choosing who to do business with.
By holding a certificate, your potential suppliers demonstrate that, from upper management down to the production floor, its organization is committed to ensuring their manufacturing facility adheres to elevated safety, quality, and sanitary practices.
By doing your due diligence up front, you can manage a system that creates a consistent quality product.
Your customers depend on it.
Check all your packaging boxes with Bedford

With BRCGS and ISO 9001:2015 certifications, Bedford offers you the confidence that your brand will receive a quality packaging solution that will be produced with food safety standards top of mind.
Request our regulatory compliance documentation when you request a quote for your next project.